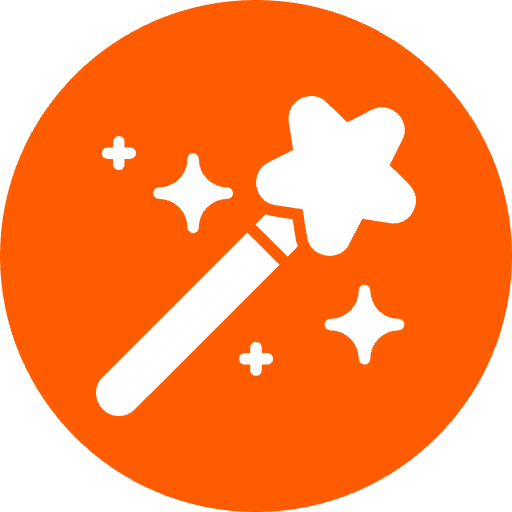
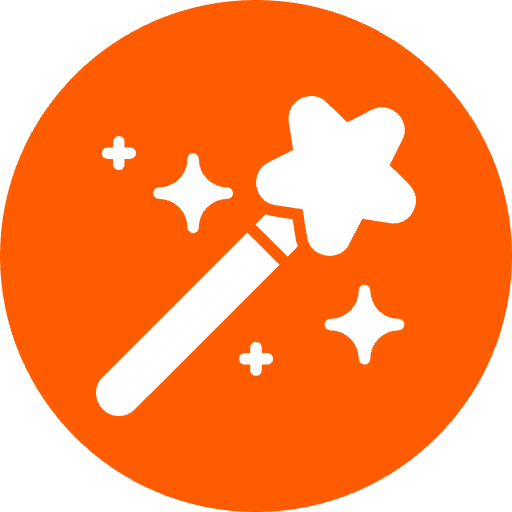
Workplace safety is non-negotiable, especially in manufacturing environments where risks are inherent. Traditionally, safety measures have relied on reactive approaches, addressing incidents after they occur. But what if we could anticipate risks and prevent accidents before they happen? That's where Artificial Intelligence (AI) is changing the game, empowering manufacturers to build proactive safety cultures and protect their most valuable assets – their people. Forward-thinking manufacturers are turning to comprehensive AI platform for business to integrate these capabilities directly into their operations.
Let's explore how AI is transforming workplace safety in manufacturing, making factories smarter and safer:
Imagine a system that analyzes historical data to identify patterns and predict potential safety hazards before they escalate. AI makes this possible:
Risk Assessment and Prevention: AI algorithms can analyze vast datasets, including incident reports, near-miss data, environmental readings, and even worker health records, to identify hidden patterns and correlations that human analysts might miss. This enables manufacturers to pinpoint potential risks associated with specific tasks, equipment, or environmental factors, allowing for targeted interventions and proactive safety measures.
Proactive Safety Measures: Rather than reacting to accidents after they happen, AI empowers proactive safety management. By identifying leading indicators of potential incidents, manufacturers can implement targeted safety training programs, modify workflows to reduce risks, and implement preventative maintenance schedules for equipment, minimizing downtime and preventing accidents before they occur.
In dynamic manufacturing environments, constant vigilance is crucial. AI provides an extra set of eyes:
Surveillance Systems: AI-powered cameras and sensors can monitor the factory floor in real-time, detecting unsafe worker behavior, identifying potential hazards like spills or obstructions, and even recognizing early warning signs of equipment failure. This real-time monitoring enables immediate intervention, preventing minor incidents from escalating into major accidents.
Anomaly Detection: AI excels at spotting anomalies that deviate from normal patterns. By continuously monitoring data streams from machinery sensors, environmental monitors, and even wearable devices, AI can detect unusual vibrations in equipment, temperature fluctuations, or changes in worker biometrics that might indicate fatigue or potential health issues. These early warnings allow for timely intervention, preventing equipment failures, reducing downtime, and most importantly, protecting worker well-being.
Effective safety training is essential, but traditional methods can be passive and unengaging. AI injects new life into safety education:
Simulation and Virtual Reality: AI-powered simulations and VR training immerse workers in realistic scenarios, allowing them to practice safety procedures, experience the consequences of unsafe actions in a risk-free virtual environment, and develop critical decision-making skills in simulated high-pressure situations. This immersive approach leads to better knowledge retention and prepares workers for real-world challenges.
Personalized Training Programs: Not all workers face the same risks or require the same training. AI enables personalized training programs based on individual job roles, skill levels, and even learning preferences. By tailoring training content to specific needs, AI ensures that workers receive the most relevant and engaging instruction, maximizing knowledge absorption and improving overall safety awareness.
Navigating complex safety regulations and maintaining meticulous documentation can be daunting. AI simplifies compliance:
Regulatory Monitoring: AI-powered systems can automatically monitor changes in safety regulations, ensuring that companies stay updated on the latest requirements and avoid costly penalties.
Documentation and Reporting: AI streamlines safety documentation and incident reporting by automating data collection, generating reports, and even identifying potential root causes of incidents, saving time, reducing errors, and providing valuable insights for continuous improvement.
Wearable technology is no longer just about fitness tracking; it's becoming an essential tool for workplace safety:
Smart Wearables: AI-powered smartwatches, glasses, and even exosuits can monitor worker vital signs, fatigue levels, posture, and proximity to hazards in real-time. This data provides personalized insights into worker well-being and allows for proactive interventions, such as recommending rest breaks, adjusting workloads, or providing immediate assistance when needed.
Alert Systems: Wearable AI can provide instant alerts to workers when they are entering hazardous areas, exceeding noise exposure limits, or engaging in risky behaviors. This real-time feedback helps workers make safer choices and avoid potential accidents.
Even with the best prevention efforts, emergencies can still happen. AI helps manufacturers prepare and respond effectively:
Emergency Response Planning: AI can analyze historical data, simulate various emergency scenarios, and recommend optimal evacuation routes, assembly points, and communication protocols, enhancing preparedness and minimizing potential chaos during an event.
Real-Time Decision Support: During an emergency, AI can provide real-time data analysis, predictive modeling, and decision support to incident commanders, enabling them to make informed decisions quickly, coordinate resources efficiently, and minimize the impact of the event.
While the potential of AI for workplace safety is immense, it's crucial to address potential challenges:
Privacy and Ethical Concerns: Transparency and ethical data handling are paramount. Employees should be informed about data collection practices, consent should be obtained when necessary, and data should be anonymized and secured to protect worker privacy.
Integration with Existing Systems: Seamless integration with existing safety systems, sensor networks, and manufacturing execution systems is essential for real-time data sharing and effective AI implementation.
Data Accuracy and Reliability: The success of AI relies on accurate and reliable data. Manufacturers need to ensure data quality, implement robust data validation processes, and address any biases in the data to avoid inaccurate predictions or recommendations.
The journey toward a safer workplace is continuous. Here's a glimpse into the future:
Emerging Trends and Innovations: We can expect even more sophisticated AI applications, such as AI-powered risk prediction models that incorporate external factors like weather patterns and supply chain disruptions, and even autonomous robots that perform hazardous tasks, reducing human exposure to risks.
Long-Term Impact on Safety Practices: AI is poised to shift safety cultures from reactive to predictive and proactive, creating a future where accidents are not just prevented, but deemed unacceptable and avoidable through the power of AI.
The integration of AI in workplace safety is not about replacing human judgment or responsibility - it's about augmenting human capabilities with data-driven insights and intelligent automation. By embracing AI, manufacturers can build safer, more efficient, and more productive workplaces where employees feel valued, protected, and empowered to do their best work without compromising their well-being. The future of manufacturing is safe, intelligent, and driven by the power of AI.