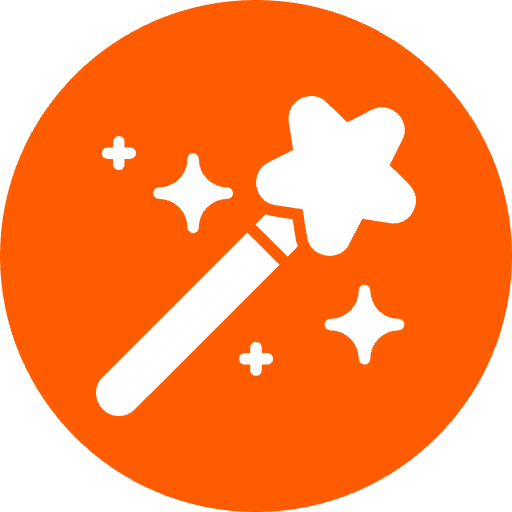
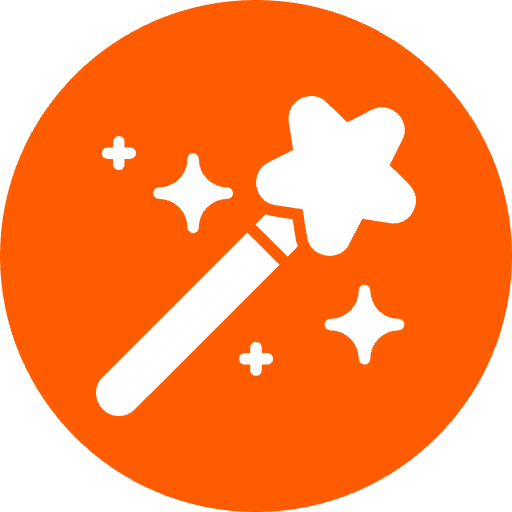
For years, businesses across a multitude of industries have grappled with the costly and often unavoidable headache of equipment downtime. Whether it’s a critical piece of machinery in a manufacturing plant or a server powering a crucial online service, unexpected failures can disrupt operations, impact revenue, and damage reputation.
While traditional maintenance approaches relied on reactive repairs or scheduled maintenance based on estimated lifespans, the emergence of AI is ushering in a new era of proactive and intelligent maintenance - one that minimizes downtime and maximizes operational efficiency.
Imagine having the ability to anticipate equipment failures before they occur, identify potential issues while they’re still in their infancy, and schedule maintenance precisely when it's needed, not based on a guesstimate or a calendar date. This is the power of AI-driven predictive maintenance.
By leveraging the combined might of sensors, Industrial Internet of Things (IIoT) devices, and machine learning algorithms, AI can:
Collect and Analyze Real-Time Data: Modern equipment, from factory machines to jet engines, can be outfitted with sensors that act like their own personal health trackers. These sensors collect a continuous stream of data on various parameters like temperature, vibration, pressure, oil levels, energy consumption, and more. AI algorithms then analyze this real-time data, identifying subtle patterns and anomalies that can indicate potential issues – often long before they’d be noticeable to even a trained human eye.
Identify Early Warning Signs: Like a seasoned doctor detecting the faintest whisper of an ailment before it manifests as a full-blown illness, AI can identify early warning signs of equipment deterioration or potential failures. This might be a slight increase in vibration, a subtle change in temperature, or a deviation in energy consumption. This early detection is crucial, allowing businesses to address issues proactively before they escalate into costly downtime events.
Predict Equipment Lifespan: Forget relying on generic lifespan estimates provided by manufacturers, which are often based on averages and ideal conditions. AI analyzes both historical data and real-time data (the current condition and performance of your specific machine) to provide accurate predictions of individual equipment lifespans. This allows businesses to optimize maintenance schedules, reduce unnecessary downtime caused by over-maintenance, and maximize the useful life of their assets, getting the most out of their investments.
The advantages of adopting AI-driven predictive maintenance extend far beyond simply reducing downtime. By shifting from a reactive to a proactive approach, businesses can unlock a ripple effect of benefits that impact their entire operation:
Significant Cost Savings: Unscheduled downtime is incredibly expensive. It leads to lost production, rushed repairs, expedited shipping costs, and potential penalties for missed deadlines. By preventing major equipment failures and reducing the need for reactive repairs, businesses can significantly reduce maintenance costs, minimize production losses, and optimize their maintenance budgets for maximum impact.
Increased Operational Efficiency: With fewer unplanned downtime events disrupting operations, businesses can achieve higher levels of productivity. Imagine a production line running smoothly without unexpected halts, or a critical server staying online without interruption. This smoother operation allows for optimal resource allocation, more accurate production forecasting, and more predictable workflows, leading to increased efficiency across the board.
Improved Safety: Safety should always be a top priority. By proactively identifying and addressing potential equipment failures, businesses can create a safer working environment for their employees. This minimizes the risk of accidents or injuries that can be caused by malfunctioning equipment, creating a more secure and confident work environment.
Enhanced Asset Management: AI-powered predictive maintenance provides a wealth of valuable data insights that go beyond simple maintenance schedules. This data allows businesses to track asset performance over time, identify trends in equipment wear and tear, optimize asset utilization, make data-driven decisions about repair, replacement, or upgrades, and ultimately maximize the return on their asset investments.
The rise of no-code AI platforms is further democratizing access to this game-changing technology. Now, businesses of all sizes, from small manufacturing operations to large-scale industrial plants, regardless of their technical expertise, can leverage the power of AI-driven predictive maintenance to optimize their operations and stay ahead of the curve.
The writing is on the wall: the future of maintenance is predictive, proactive, and powered by AI. The question is, are you ready to embrace the future and transform your approach to maintenance, reaping the rewards of increased efficiency, reduced costs, and improved safety? Or will you be left behind, grappling with the avoidable costs and disruptions of downtime in an increasingly competitive world? The choice, and the future, are yours.