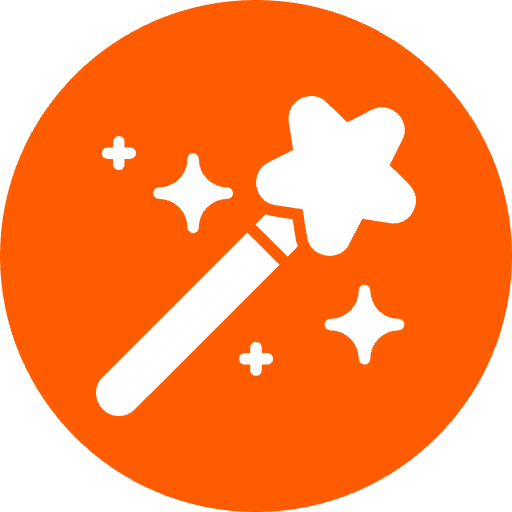
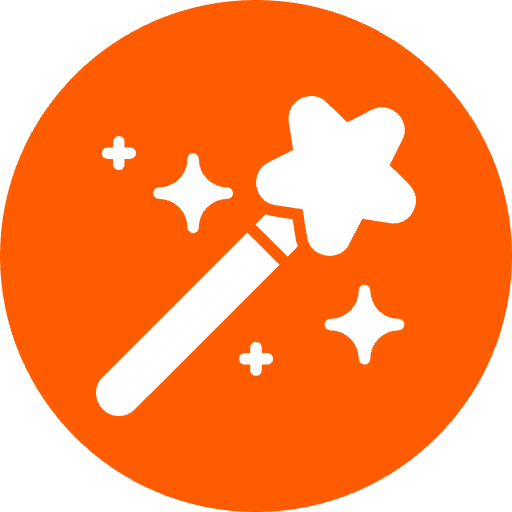
There are four main maintenance strategies that wind turbine operations teams and technicians can use in general with their hardware: reactive, preventive, predictive, and reliability-centered. Each strategy has its own merits and demerits, and the choice of strategy will depend on the specific circumstances.
Reactive maintenance is the strategy of repairing parts or equipment only after they have broken down or been run to the point of failure. The main merit of this strategy is that it offers maximum utilization and in turn maximum production output of the asset by using it to its limits. However, the main demerit is that it can lead to unexpected downtime and increased costs due to unplanned repairs.
Preventive maintenance is the strategy of scheduled regular checks, cleaning, and replacement of parts based on a predetermined schedule. The main merit of this strategy is that it can prevent component failure and downtime. However, the main disadvantage is that it can lead to unnecessary replacement of parts and increased costs.
Predictive maintenance is the strategy of using data, such as vibration and temperature measurements, to determine the health of the turbine and schedule maintenance before component failure occurs. The main merit of this strategy is that it limits unplanned downtime and increases the lifespan of equipment. Additionally, it can be cheaper than preventive maintenance. The main demerit is that it requires a significant investment in data collection and analysis.
Reliability-centered maintenance is the strategy of identifying hidden areas of risk by looking at each asset individually and determining how, should that asset fail, it would affect other equipment and systems. The main merit of this strategy is that it allows for the identification of hidden areas of risk. The main demerit is that it requires a significant investment in time and resources to implement.
In case of wind turbines, the typical distribution of issues detected is still around 55% reactive, 31% preventive, 12% predictive and the very minor remaining portion is reliability-centered. This leads to higher frequency of unscheduled maintenance, higher maintenance costs, unanticipated downtime and opportunity loss for wind farms.So why is it that wind farms fall into this trap of working with an ineffective maintenance strategy?
One reason why the maintenance strategies rely on being reactive is the simple foundational idea that you can run the machine until it is working. However, the flip side is that there is a higher chance that turbines wear out much faster or that there are catastrophic failures of equipment. Often, this is seen as a trade-off between investing in a better maintenance strategy and maximizing short-term returns. Whereas the reality is that an investment in better maintenance strategy is non-negotiable - reliable equipment over long-term maximizes business benefits.
The other reason why the maintenance strategy in new wind farms begins with being reactive is because of a belief that new equipment is less likely to break down. While that may be true to some extent, not taking initiative in adopting a better maintenance strategy means that there are no lessons from maintenance incidents and history of the machines. Often, the way to keep machines in reliable mode of operation is pinned on predictive maintenance strategies involving AI learning when the equipment works efficiently, how they show signs of wear, and how either reactive or preventive strategies of maintenance impact the life of the equipment.
The third and the most common reason to overlook an immediate implementation of predictive maintenance and making a move towards reliability-centered maintenance strategies is that the cost of maintenance is within acceptable thresholds, or that the failures of turbines are not alarming. And therefore any investment in maintenance is seen to be unnecessary. However, this line of reasoning is worrisome because the cost of maintenance is by default escalating all the time, and the only way to keep it in check is to invest in better maintenance strategies.
So, when is it the right time to invest in predictive maintenance and make a move towards reliability-centered maintenance strategy? If you haven’t done it already, it is NOW.